高能束流加工技術在航空發動機領域的應用
2013年09月13日 10:06點擊:2269作者:默認來源:>>進入該公司展臺
【中國機床商務網】導讀:高能束流加工技術是21世紀zui重要的*制造技術之一,具有非接觸、能量可控、材料適應性廣、柔性強、質量優、資源節約、環境友好等綜合優勢,既可用于大批量自動化生產,又適用于多品種、小批量加工,甚至個性化產品的定制,因此成為傳統制造業改造升級*的重要技術。高能束流加工技術在工業中所占的比重已成為衡量一個國家工業制造水平高低的重要指標之一,是研制生產高、精、尖武器裝備的關鍵技術,對保障國家安全具有重要意義。經過多年的發展,高能束流加工技術已經發展為焊接、切割、制孔、快速成形、刻蝕、微納加工、表面改性、噴涂及氣相沉積等多種門類,在航空航天、船舶、兵器、核能、交通、醫療等諸多領域發揮著重要的作用。
本文將以高能束流加工技術在航空發動機領域的應用為背景,重點介紹高能束焊接、高能束快速成形和高能束表面工程技術當前的應用情況,同時,針對新型發動機技術新需求,闡述高能束流加工技術在航空制造中的發展趨勢。
高能束流焊接技術及其應用
高能束焊接在提高材料利用率、減輕鈦合金結構重量、降低成本方面*優勢,這使得以高能束流為熱源的*焊接技術——電子束焊接、激光焊接、電子束復合焊接、激光復合熱源焊接技術在航空領域得到廣泛應用[4-6],而在發動機制造上,高能束焊接也有重要應用。
激光焊接是以高能量密度的激光束流為加熱熱源,實現材料原子間結合的連接技術。由于其熱源能量密度高、加熱集中,焊縫深寬比大、焊接速度快、焊接變形小、焊縫質量高,因此易于實現材料的高速、和高質量焊接。在發動機上,主要用于零部件焊接與修復上,其修復技術利于近凈成形,減少裂紋產生,已應用的有航空發動機渦輪葉片、導向葉片和氣路封嚴系統的零部件[7],如:歐盟第六框架研究項目AROSATEC就開展了壓氣機定子與葉柵、高壓和低壓葉片出口與蓋板連接,以及渦輪機匣的激光焊接技術研究。美國通用公司成功地完成了噴氣發動機的導流板和導向葉片的激光焊接組裝,有效地解決了鎳基合金小型零件激光焊接變形與裂紋等問題。美國霍尼韋爾公司修復的葉片已累計飛行2000萬個飛行小時。美國伍德集團公司利用激光粉末合金熔焊技術可以修理過去認為不可修的單晶和DS合金零部件。
電子束焊接是利用高速電子會聚形成的電子束流轟擊工件產生的熱能使被焊金屬熔合的一種焊接方法。與常規電弧焊方法相比,電子束焊接具有焊縫熔深大、熔寬小、焊縫純度高的特點,多用于高質量要求結構的焊接,既可實現復雜薄壁結構焊接,也可實現大厚度金屬結構焊接[8]。自2000年以來,國內電子束焊接技術發展較為迅速,國內先后開發了脈沖電子束焊接、精密偏擺掃描電子束焊接(圖1)、電子束填絲焊接(圖2)、電子束復合焊接(圖3)等新型工藝[9],有效解決了高強度鋼、高溫鈦合金和金屬間化合物等難熔低塑性金屬材料及其結構的焊接性問題,同時達到改善焊接結構應力分布與變形精度控制、提高焊接接頭力學性能的目標。電子束焊接在航空發動機上的典型應用主要為:發動機風扇與壓氣機轉子部件、承力機匣組件、傳動齒輪系統、柔性軸與波紋管結構、鈦合金燃料貯箱等部件。

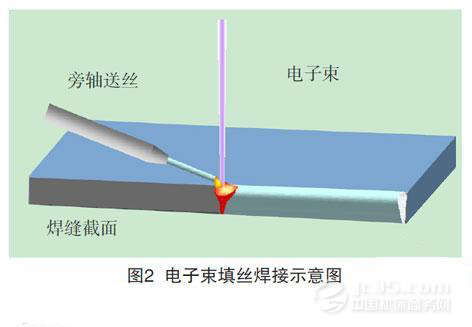
高能束流快速成形技術及其應用
激光/電子束精密增材成形技術(其原理見圖4)是一種基于離散堆積成形思想的*制造技術,無需模具,通過把零件3D模型沿一定方向離散成一系列有序的微米量級薄層,以激光或電子束為熱源,根據每層輪廓信息逐層熔化金屬粉末,直接制造出任意復雜形狀的零件,特別適合曲面型腔、懸空薄壁以及變截面等復雜結構制造,無需數控加工,僅需熱處理和表面光整零件即可;具有大幅減少制造工序、縮短生產周期,節省材料及經費等特點,在航空航天、核工業、兵器等新型號研制、現役型號技術升級上具有廣闊的應用前景[9-11]。該技術根據材料在沉積時的不同狀態可以分為:熔覆沉積技術,材料在沉積反應時才送入沉積位置,由高能束在沉積區域產生熔池并高速移動,熔化后沉積下來;選區沉積技術,材料在沉積反應前已位于沉積位置上,再用高能束逐點逐行燒結或熔化。
激光同軸送粉快速成形技術可用于航空發動機機匣、封嚴結構、修復鈦合金葉片和整體葉盤等構件,且其力學性能達到鍛件的水平。其相關成果已應用在武裝直升機、AIM導彈、波音7X7客機、F/A-18E/F及F22戰機上。高能束選區熔化自由成形技術則可應用于鈦合金整體葉盤精密成形、發動機點陣夾芯超冷結構(夾心葉片)、復雜型腔結構(燃燒室)等零部件精密成形,如圖5所示。
目前高推重比發動機的研發,使得航空發動機鈦合金葉片和輪盤的載荷條件更加苛刻,其不同位置載荷條件差異更大,單體鈦合金整體葉盤已難以滿足工況需求,迫切需要雙性能整體葉盤及其制造技術研究。高能束快速成形技術使這種雙性能整體葉盤制造成為可能。2011年,德國FraunhoferILT成功利用激光快速成形法制造了In718鎳基合金高壓氣機整體葉盤,該整體葉盤無缺陷,通過熱處理調控組織,其力學性能與鍛件相當,而且可節省材料60%,使buy-to-fly的比例從5∶1降低到2∶1,時間節省30%,目前進一步相關基礎工作正在進行。
高能束流表面工程技術及其應用
隨著高推重比發動機的研發,其使用環境越來越苛刻,使用壽命和可靠性要求也越來越高,如:美國新型發動機壽命達到3000h,大型軍用運輸機、客機發動機壽命達到數萬小時,未來軍用發動機空中停車率為0.01‰~0.06‰飛行小時,民用發動機為0.002‰~0.02‰飛行小時,由上述數據可以斷定如想提高發動機使用壽命和可靠性,單純依靠材料本身性能已不能滿足要求,因此必須對相關零件進行表面防護。高能束流表面工程技術主要利用激光、電子束、離子束及等離子體等高能量密度束流使材料表面改性或在材料的表面形成防護或功能涂層,以提高零件的壽命或使用性能。
高能束表面改性加工技術,主要包括激光沖擊強化、離子注入及表面完整性技術等,在激光沖擊強化方面,歐美等發達國家的技術已經較為成熟,已應用于F101、F110、F414和F/A-22等發動機葉片上,GE公司自1997年直到目前累計強化葉片100000片以上,提高葉片高周疲勞壽命5~6倍,截止2008年底,波音公司和空客公司的寬弦風扇葉片強化數量超過35000片。在離子注入方面,美歐國家已實現一些軍工零部件上的應用。如:莫斯科航空研究所用離子注入技術處理鈦合金壓氣機葉片,使葉片的疲勞強度提高5%~20%,耐熱氣腐蝕的性能提高2倍以上,耐顆粒沖蝕的性能提高20%~50%,耐壓縮氣體沖蝕的性能提高3倍以上[12]。
高能束涂層技術主要包括電子束物理氣相沉積、大氣/真空等離子噴涂、超音速火焰噴涂、冷噴涂、真空電弧沉積和磁控濺射等。制備的涂層按功能可以分為:熱障涂層、高溫抗氧化涂層、阻燃涂層、環境障礙涂層、封嚴涂層、耐磨涂層、耐腐蝕涂層、抗沖刷涂層、抗微動磨損涂層、憎水涂層、隱身涂層等。熱障涂層應用于發動機的高溫金屬部件上,如燃燒室、渦輪葉片、尾噴管等,用來提高這些部件的使用溫度和壽命[13-14]。高溫抗氧化涂層應用于燃燒室和渦輪葉片等,用來提高這些部件的抗高溫氧化和熱腐蝕性能。阻燃涂層應用于鈦合金制成的壓氣機轉子葉片和機匣內環,防止鈦火事故的發生。封嚴涂層應用于壓氣機葉片、渦輪葉片與外環機匣之間,用來控制部件運轉間隙,以減少氣體泄漏、增加喘振裕度、降低油耗、提高壓氣機和渦輪效率[15]。耐磨耐腐蝕涂層應用于摩擦磨損零件,如軸、軸承、柱塞等,以提高這些零件的使用壽命??箾_蝕涂層應用于風扇和壓氣機葉片,提高葉片抗沙塵、雨滴的沖刷和海洋環境鹽霧的腐蝕??刮幽p涂層應用于葉片的榫頭和榫槽、螺栓聯接、鉚釘聯接、鍵或銷聯接等接觸表面,提高抗表面疲勞損傷壽命。憎水涂層通過制備超疏水結構的涂層,使涂層與水的接觸角變大,從而達到防止結冰的作用,提高飛行器的安全。隱身涂層應用于進氣機匣、尾噴管等部位,以降低紅外輻射或雷達波反射截面。國外高能束涂層技術在發動機應用部位如圖6所示。
高能束流其他加工技術及其應用
磨粒流加工是采用半固態的有機高分子材料作為載體,將具有刮削作用的磨粒懸浮在其中,形成粘彈性磨料,在壓力作用下流動的磨粒流介質擠擦流過工件表面從而實現對工件表面的光整精加工。在航空發動機上,該技術主要用于發動機葉片、葉輪、整體葉盤等去毛刺和拋光,如:美國通用電氣公司在T700發動機的壓氣機*級整體葉盤加工過程中就已經由原來的手工打磨采用磨粒流的方法來拋光。數控銑削加工后,葉片表面粗糙度Ra為2μm,采用磨粒流拋光后葉片表面粗糙度Ra達到0.4μm。
激光微孔制造技術作為一種*制造技術,具有高精的優勢,已應用于航空發動機渦輪葉片、導向葉片、噴嘴、外罩以及燃燒室等熱端部件的冷卻孔制造。其加工孔徑為0.1~1.5mm,孔深為0.5~5mm,大部分微孔分布在3D復雜型面上,空間分布位置復雜,并且微孔軸線與表面夾角小,形成復雜的斜孔?,F代航空發動機為了提高熱端部件耐高溫能力,采用熱障涂層等多層材料結構以及*的表面防護涂層技術,這為直接對這些零部件進行微孔制造帶來了更大的難度。隨著超快激光技術的突破,尤其是飛秒激光技術的快速發展,為這一難題的解決提供了新的有效手段,為超快激光陶瓷涂層制孔技術在航空中的應用奠定基礎。
結束語
隨著技術的更新與發展,高能束流加工已不再是一種單純意義上的加工制造技術,已發展成為高能束流能量場與品質、材料冶金、結構力學、自動化、計算機等多學科集成的工程制造技術,顯現出*的技術附加值。高能束流加工技術的發展方向更趨于加工過程的自動化和智能化、虛擬制造、復合束源和集成化,并向著高品質、高功率、率、多功能和結構功能一體化方向發展,同時隨著其在航空發動機及其他領域的應用愈加廣泛和成熟,高能束流加工技術必將為我國航空事業的進步做出更大貢獻。(本文所配封面圖由德國Fraunhofer激光技術研究所提供)
(文章來源:航空制造網)
本文將以高能束流加工技術在航空發動機領域的應用為背景,重點介紹高能束焊接、高能束快速成形和高能束表面工程技術當前的應用情況,同時,針對新型發動機技術新需求,闡述高能束流加工技術在航空制造中的發展趨勢。
高能束流焊接技術及其應用
高能束焊接在提高材料利用率、減輕鈦合金結構重量、降低成本方面*優勢,這使得以高能束流為熱源的*焊接技術——電子束焊接、激光焊接、電子束復合焊接、激光復合熱源焊接技術在航空領域得到廣泛應用[4-6],而在發動機制造上,高能束焊接也有重要應用。
激光焊接是以高能量密度的激光束流為加熱熱源,實現材料原子間結合的連接技術。由于其熱源能量密度高、加熱集中,焊縫深寬比大、焊接速度快、焊接變形小、焊縫質量高,因此易于實現材料的高速、和高質量焊接。在發動機上,主要用于零部件焊接與修復上,其修復技術利于近凈成形,減少裂紋產生,已應用的有航空發動機渦輪葉片、導向葉片和氣路封嚴系統的零部件[7],如:歐盟第六框架研究項目AROSATEC就開展了壓氣機定子與葉柵、高壓和低壓葉片出口與蓋板連接,以及渦輪機匣的激光焊接技術研究。美國通用公司成功地完成了噴氣發動機的導流板和導向葉片的激光焊接組裝,有效地解決了鎳基合金小型零件激光焊接變形與裂紋等問題。美國霍尼韋爾公司修復的葉片已累計飛行2000萬個飛行小時。美國伍德集團公司利用激光粉末合金熔焊技術可以修理過去認為不可修的單晶和DS合金零部件。
電子束焊接是利用高速電子會聚形成的電子束流轟擊工件產生的熱能使被焊金屬熔合的一種焊接方法。與常規電弧焊方法相比,電子束焊接具有焊縫熔深大、熔寬小、焊縫純度高的特點,多用于高質量要求結構的焊接,既可實現復雜薄壁結構焊接,也可實現大厚度金屬結構焊接[8]。自2000年以來,國內電子束焊接技術發展較為迅速,國內先后開發了脈沖電子束焊接、精密偏擺掃描電子束焊接(圖1)、電子束填絲焊接(圖2)、電子束復合焊接(圖3)等新型工藝[9],有效解決了高強度鋼、高溫鈦合金和金屬間化合物等難熔低塑性金屬材料及其結構的焊接性問題,同時達到改善焊接結構應力分布與變形精度控制、提高焊接接頭力學性能的目標。電子束焊接在航空發動機上的典型應用主要為:發動機風扇與壓氣機轉子部件、承力機匣組件、傳動齒輪系統、柔性軸與波紋管結構、鈦合金燃料貯箱等部件。

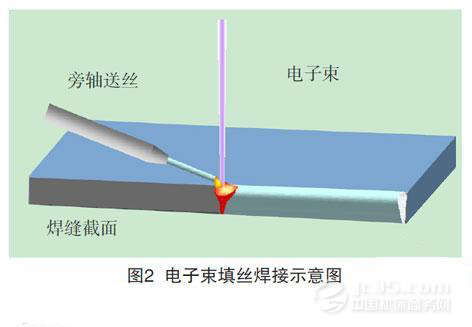

高能束流快速成形技術及其應用
激光/電子束精密增材成形技術(其原理見圖4)是一種基于離散堆積成形思想的*制造技術,無需模具,通過把零件3D模型沿一定方向離散成一系列有序的微米量級薄層,以激光或電子束為熱源,根據每層輪廓信息逐層熔化金屬粉末,直接制造出任意復雜形狀的零件,特別適合曲面型腔、懸空薄壁以及變截面等復雜結構制造,無需數控加工,僅需熱處理和表面光整零件即可;具有大幅減少制造工序、縮短生產周期,節省材料及經費等特點,在航空航天、核工業、兵器等新型號研制、現役型號技術升級上具有廣闊的應用前景[9-11]。該技術根據材料在沉積時的不同狀態可以分為:熔覆沉積技術,材料在沉積反應時才送入沉積位置,由高能束在沉積區域產生熔池并高速移動,熔化后沉積下來;選區沉積技術,材料在沉積反應前已位于沉積位置上,再用高能束逐點逐行燒結或熔化。

激光同軸送粉快速成形技術可用于航空發動機機匣、封嚴結構、修復鈦合金葉片和整體葉盤等構件,且其力學性能達到鍛件的水平。其相關成果已應用在武裝直升機、AIM導彈、波音7X7客機、F/A-18E/F及F22戰機上。高能束選區熔化自由成形技術則可應用于鈦合金整體葉盤精密成形、發動機點陣夾芯超冷結構(夾心葉片)、復雜型腔結構(燃燒室)等零部件精密成形,如圖5所示。

目前高推重比發動機的研發,使得航空發動機鈦合金葉片和輪盤的載荷條件更加苛刻,其不同位置載荷條件差異更大,單體鈦合金整體葉盤已難以滿足工況需求,迫切需要雙性能整體葉盤及其制造技術研究。高能束快速成形技術使這種雙性能整體葉盤制造成為可能。2011年,德國FraunhoferILT成功利用激光快速成形法制造了In718鎳基合金高壓氣機整體葉盤,該整體葉盤無缺陷,通過熱處理調控組織,其力學性能與鍛件相當,而且可節省材料60%,使buy-to-fly的比例從5∶1降低到2∶1,時間節省30%,目前進一步相關基礎工作正在進行。
高能束流表面工程技術及其應用
隨著高推重比發動機的研發,其使用環境越來越苛刻,使用壽命和可靠性要求也越來越高,如:美國新型發動機壽命達到3000h,大型軍用運輸機、客機發動機壽命達到數萬小時,未來軍用發動機空中停車率為0.01‰~0.06‰飛行小時,民用發動機為0.002‰~0.02‰飛行小時,由上述數據可以斷定如想提高發動機使用壽命和可靠性,單純依靠材料本身性能已不能滿足要求,因此必須對相關零件進行表面防護。高能束流表面工程技術主要利用激光、電子束、離子束及等離子體等高能量密度束流使材料表面改性或在材料的表面形成防護或功能涂層,以提高零件的壽命或使用性能。
高能束表面改性加工技術,主要包括激光沖擊強化、離子注入及表面完整性技術等,在激光沖擊強化方面,歐美等發達國家的技術已經較為成熟,已應用于F101、F110、F414和F/A-22等發動機葉片上,GE公司自1997年直到目前累計強化葉片100000片以上,提高葉片高周疲勞壽命5~6倍,截止2008年底,波音公司和空客公司的寬弦風扇葉片強化數量超過35000片。在離子注入方面,美歐國家已實現一些軍工零部件上的應用。如:莫斯科航空研究所用離子注入技術處理鈦合金壓氣機葉片,使葉片的疲勞強度提高5%~20%,耐熱氣腐蝕的性能提高2倍以上,耐顆粒沖蝕的性能提高20%~50%,耐壓縮氣體沖蝕的性能提高3倍以上[12]。
高能束涂層技術主要包括電子束物理氣相沉積、大氣/真空等離子噴涂、超音速火焰噴涂、冷噴涂、真空電弧沉積和磁控濺射等。制備的涂層按功能可以分為:熱障涂層、高溫抗氧化涂層、阻燃涂層、環境障礙涂層、封嚴涂層、耐磨涂層、耐腐蝕涂層、抗沖刷涂層、抗微動磨損涂層、憎水涂層、隱身涂層等。熱障涂層應用于發動機的高溫金屬部件上,如燃燒室、渦輪葉片、尾噴管等,用來提高這些部件的使用溫度和壽命[13-14]。高溫抗氧化涂層應用于燃燒室和渦輪葉片等,用來提高這些部件的抗高溫氧化和熱腐蝕性能。阻燃涂層應用于鈦合金制成的壓氣機轉子葉片和機匣內環,防止鈦火事故的發生。封嚴涂層應用于壓氣機葉片、渦輪葉片與外環機匣之間,用來控制部件運轉間隙,以減少氣體泄漏、增加喘振裕度、降低油耗、提高壓氣機和渦輪效率[15]。耐磨耐腐蝕涂層應用于摩擦磨損零件,如軸、軸承、柱塞等,以提高這些零件的使用壽命??箾_蝕涂層應用于風扇和壓氣機葉片,提高葉片抗沙塵、雨滴的沖刷和海洋環境鹽霧的腐蝕??刮幽p涂層應用于葉片的榫頭和榫槽、螺栓聯接、鉚釘聯接、鍵或銷聯接等接觸表面,提高抗表面疲勞損傷壽命。憎水涂層通過制備超疏水結構的涂層,使涂層與水的接觸角變大,從而達到防止結冰的作用,提高飛行器的安全。隱身涂層應用于進氣機匣、尾噴管等部位,以降低紅外輻射或雷達波反射截面。國外高能束涂層技術在發動機應用部位如圖6所示。

高能束流其他加工技術及其應用
磨粒流加工是采用半固態的有機高分子材料作為載體,將具有刮削作用的磨粒懸浮在其中,形成粘彈性磨料,在壓力作用下流動的磨粒流介質擠擦流過工件表面從而實現對工件表面的光整精加工。在航空發動機上,該技術主要用于發動機葉片、葉輪、整體葉盤等去毛刺和拋光,如:美國通用電氣公司在T700發動機的壓氣機*級整體葉盤加工過程中就已經由原來的手工打磨采用磨粒流的方法來拋光。數控銑削加工后,葉片表面粗糙度Ra為2μm,采用磨粒流拋光后葉片表面粗糙度Ra達到0.4μm。
激光微孔制造技術作為一種*制造技術,具有高精的優勢,已應用于航空發動機渦輪葉片、導向葉片、噴嘴、外罩以及燃燒室等熱端部件的冷卻孔制造。其加工孔徑為0.1~1.5mm,孔深為0.5~5mm,大部分微孔分布在3D復雜型面上,空間分布位置復雜,并且微孔軸線與表面夾角小,形成復雜的斜孔?,F代航空發動機為了提高熱端部件耐高溫能力,采用熱障涂層等多層材料結構以及*的表面防護涂層技術,這為直接對這些零部件進行微孔制造帶來了更大的難度。隨著超快激光技術的突破,尤其是飛秒激光技術的快速發展,為這一難題的解決提供了新的有效手段,為超快激光陶瓷涂層制孔技術在航空中的應用奠定基礎。
結束語
隨著技術的更新與發展,高能束流加工已不再是一種單純意義上的加工制造技術,已發展成為高能束流能量場與品質、材料冶金、結構力學、自動化、計算機等多學科集成的工程制造技術,顯現出*的技術附加值。高能束流加工技術的發展方向更趨于加工過程的自動化和智能化、虛擬制造、復合束源和集成化,并向著高品質、高功率、率、多功能和結構功能一體化方向發展,同時隨著其在航空發動機及其他領域的應用愈加廣泛和成熟,高能束流加工技術必將為我國航空事業的進步做出更大貢獻。(本文所配封面圖由德國Fraunhofer激光技術研究所提供)
(文章來源:航空制造網)
上一篇:寶瑪水基工作液優勢介紹
下一篇:金屬材料的激光切割應用分析
- 凡本網注明"來源:機床商務網"的所有作品,版權均屬于機床商務網,轉載請必須注明機床商務網,//www.hzzhongling.com/。違反者本網將追究相關法律責任。
- 企業發布的公司新聞、技術文章、資料下載等內容,如涉及侵權、違規遭投訴的,一律由發布企業自行承擔責任,本網有權刪除內容并追溯責任。
- 本網轉載并注明自其它來源的作品,目的在于傳遞更多信息,并不代表本網贊同其觀點或證實其內容的真實性,不承擔此類作品侵權行為的直接責任及連帶責任。其他媒體、網站或個人從本網轉載時,必須保留本網注明的作品來源,并自負版權等法律責任。
- 如涉及作品內容、版權等問題,請在作品發表之日起一周內與本網聯系,否則視為放棄相關權利。